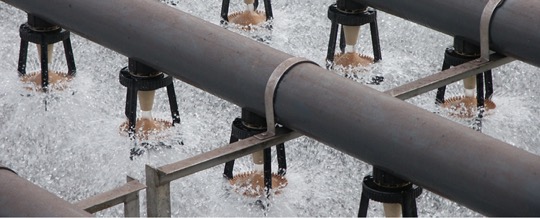
Complete guide to establishing an optimal water treatment system for cooling towers
- What is the purpose of an automatic contribution system?
- What is the role of an appropriate chemical treatment?
- How to keep the circulating water within the optimal operating limits?
- And why is it useful to use osmosed water during the water treatment phase?
Introduction to the operation of the cooling tower
Cooling the water by using evaporative towers is a very energy efficient system. By forcing a small amount of water to evaporate, the temperature of the rest of the circulating water mass is reduced.
The amount of water evaporated to its maximum potential is, indicatively, 2% of the total circulating water mass. Therefore, the use of the latent evaporation heat allows to work at temperatures close to the wet bulb temperatures and therefore to achieve very low operating costs compared to cooling by means of chillers or tap water.
What happens to the water in circulation?
The cooling system of the cooling tower cannot be considered a completely closed circuit, as there is a direct exchange with the air, nor a completely open circuit as most of the water is recirculated.
Due to the evaporation of the water, it is necessary to provide an automatic supply system that maintains the correct water level.
In comparison with the replacement water, the water in circulation is mainly subject to the following phenomena that can change the initial quality:
Factors that come into play water quality
- Dirt and contamination due to contact with the air: to achieve evaporation, large masses of air are introduced into the fill, causing the tower to clean and remove dust from the incoming air that may contain dirt, organic matter and possibly contaminants.
- Dirt and contamination due to the contact with the equipment to be cooled and possibly with the direct cooling of the parts.
- Continuous increase of the salt concentration in the water, including the above mentioned contaminating elements. Due to the evaporation of part of the water, which can be considered distilled, and its consequent composition, the salinity of the water in circulation would continue to increase, without adequate purging.
- Increased bacterial load and algae/biofilm growth due to favourable conditions (light, organic matter, temperature, oxygen level)
Benefits of using an automatic water treatment system
Without proper management and chemical treatment, the circulating water would quickly lead to negative phenomena in the cooling system and would decrease the exchange efficiency of both the tower and the entire circuit.
These negative phenomena can mainly be summarized as follows
Incrustations, both generalized and especially on the exchange surfaces. It should be noted that the formation of a small film of dirt would insulate the exchange surfaces involved (which have a high thermal conductivity), suddenly reducing the efficiency of the system. Over time, the dirt would increase the film, until it became a thick, insulating layer, which would clog the fillers and the cooling tower.
Localised or generalised corrosion. In addition to occurring by direct contact with the cooling water, corrosion can also occur underneath scale deposits (under-deposit corrosion). This phenomenon is very dangerous for the system, as it risks damaging the equipment and therefore causing unscheduled cooling down time.
The development of algae and biofilms, which reduce the efficiency of heat exchange, can obstruct the steps and cause health problems. The guidelines now expressly require that the system be managed optimally from the point of view of controlling bacterial growth.
It should be noted that these phenomena increase their effect when they occur simultaneously. Therefore, in order to maintain a safe and efficient management in time, it is important to operate the plant in an optimal way with respect to all parameters.
How they perform proper water treatment
The aim of the treatment is to keep the water circulating within the optimum management limits, obtaining the best compromise between results, safety and management costs. Therefore, there is no “universal” treatment system, but different configurations and degrees of complexity are possible based on:
- Size and potential of the plant. In general, small plants require simpler systems, while large plants require more complex systems.
- Degree of automation required to minimize the work of the personnel involved.
- Need for automatic adjustment according to changes in thermal load.
- Budget foreseen for the treatment system and for the subsequent management: in general, the more complex and complete systems allow management savings, therefore, they are indicated in a medium/large potential and with an important number of working hours/year, conversely, the simpler systems provide a lower purchase cost and are indicated in systems with low potential or occasional use.
- Type of process, operating conditions and quality of water supply
- Specific needs (e.g. required by the process or by the manufacturer of the equipment to be cooled)
Functions of the water treatment system
To achieve complete control of the plant, the treatment system must primarily perform the following tasks:
- Control and maintenance of the correct concentration of salt in water For this purpose, it is necessary to install an automatic purge system. It must be implemented with different operating strategies according to different demands and operating conditions, keeping the water concentration within the limits manageable by the treatment.
- Control and minimize the risks of incrustations. To protect against scale, it is important to adopt and achieve synergy between the automatic purge system, the chemical conditioning product and the water pre-treatment system, if present.
- Control and minimize corrosion risks. To avoid corrosion, it is important to adopt and achieve synergy between the automatic purge system, the chemical conditioning product and to properly select the system’s construction materials.
- Control of bacterial growth. To protect against algae and biofilm growth and to maintain acceptable operating conditions, it is important that the use of the disinfectant product is supported by materials and construction choices to minimize this phenomenon.
Softening procedures
As we have mentioned, it is advisable to equip the system with a pre-treatment of the water, such as softening or osmotization processes.
In general, the best compromise between results, operating costs and reduction of consumption is obtained through a suitable softening system that can totally or partially reduce the hardness of the water, thus allowing for more intense cycles of concentration.
In this way, it is possible to reduce water and product consumption and, at the same time, thanks to the higher concentration, to obtain more effective protection of the system and increase safety against negative effects in the event of failure of part of the treatment.
Pre-treatment and concentration factor
The following graph compares the general water consumption, taking into account hard, soft or osmosis water. It is clearly shown that a lower total water consumption is obtained by using soft water. This is achieved due to the good concentration ratio that can be obtained and the low water required for resin regeneration.
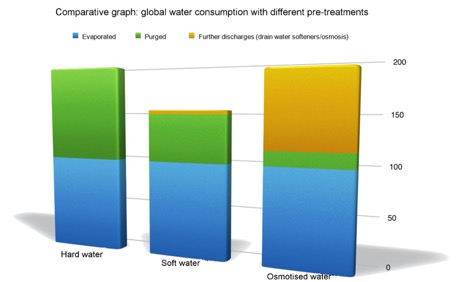
In contrast, the osmosis water supply solution is theoretically optimal if only the water volumes in the tower are considered. However, the substantial impact of the wastewater due to the osmosis process brings the overall consumption closer to that which can be obtained from hard water.
With regard to the osmosis water supply, the significant consumption of electricity and anti-precipitants must also be taken into account. Therefore, the use of osmosed water in a tower is only advisable when it is technically necessary and indispensable.
The water concentration factor
The water concentration factor of the circuit is the ratio between the water for replenishment and the water purged from the system and directly influences the quality of the water in the circuit, its consumption and chemicals. It depends on several elements:
The most important are undoubtedly the quality of the water supply (strongly influenced by the pre-treatment), the operating conditions and the type/quality/quantity of conditioning products used. In general, if no specific limits are established for the plant, the concentration factor must allow the salts present to be kept in solution, avoiding their precipitation, taking into account the elements mentioned.
For information purposes, the achievable concentration factors, under average conditions of temperature and water quality, are between 1.5 and 2.0 times for hard water, between 2.5 and 3.2 times for soft water, and between 5.0 and 8.0 times for osmotic water.
The waters in the area are very different from each other, therefore, it is not possible to define a management line as unique and unambiguous. Therefore, an overall assessment of the system should be made to determine the best approach.
One aspect to consider when choosing the type of supply is also the consumption of conditioning products, which significantly influences the plant’s operating costs. A comparative chart of the various solutions is shown below:
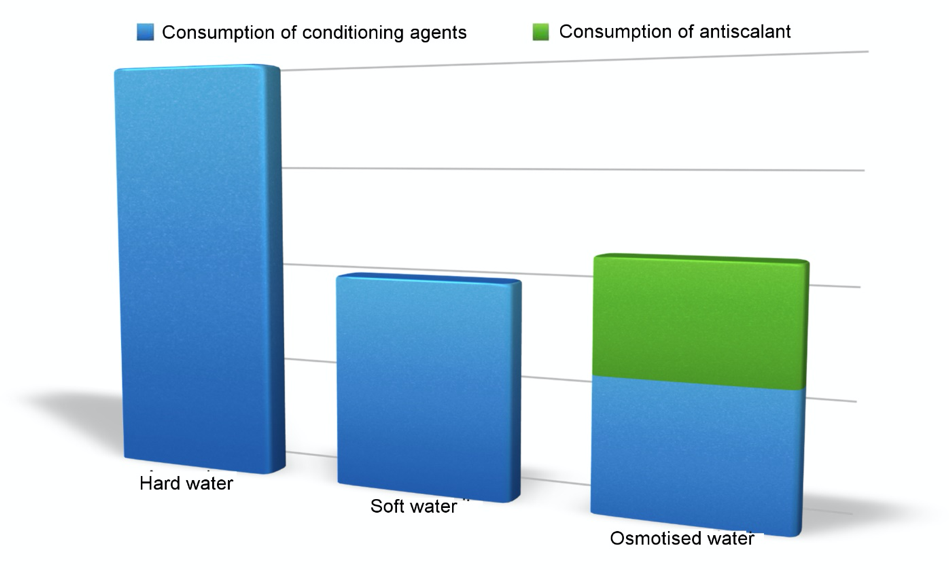
The graph shows that the use of soft or osmosed water results in a significant saving in total chemical quantities, compared to the use of hard water. For information purposes, if hard water is used in the circuit, the treatment system as a whole will be more focused on reducing the fouling factor, compared to the corrosive effect due to water in the circuit, and vice versa if soft or osmosed water is used.
Conclusions
The installation and optimal management of a suitable treatment system guarantees stable operating conditions for the cooling system and high time efficiency. Thanks to the automatic systems provided, a better management of the cooling tower is possible with a reduced operational effort.
By properly evaluating the specific requests of each plant, it is possible to foresee the right management system, with different degrees of complexity, to allow the required performances at an acceptable operating cost.
Despite the higher initial cost, the adoption of more comprehensive treatment and pre-treatment systems reduces the system’s operating costs. Therefore, they are always recommended when the average thermal capacity of the plant begins to have a high impact.